——膜集成技術(shù)
1、鉛酸蓄電池生產(chǎn)行業(yè)現(xiàn)狀
目前國(guó)內(nèi)游電池極板生產(chǎn)線的蓄電池生產(chǎn)廠家主要面臨三面的環(huán)保壓力—廢氣、廢水、和固體廢物。一般每生產(chǎn)1000個(gè)電池會(huì)產(chǎn)生63.2kg鉛塵。另外,在鉛酸蓄電池化成工序中,會(huì)產(chǎn)生硫酸霧,廢棄的化成液及清洗極片的廢水也含有一定濃度的硫酸,涂板工序、化成工序以及電池清洗工序會(huì)產(chǎn)生含鉛的重金屬?gòu)U水。
2、工藝特點(diǎn)
設(shè)備為全封閉運(yùn)行,生產(chǎn)環(huán)境好;是清潔生產(chǎn)的典型設(shè)備。
將分離、濃縮、清洗有機(jī)的集成一體,安裝使用方便。
自動(dòng)化程度高,占地面積小。
不需加入化學(xué)助劑,污泥量極少。
選用陶瓷膜和進(jìn)口耐酸,使用壽命長(zhǎng)。
具有加藥清洗功能,可對(duì)膜進(jìn)行自動(dòng)清洗,能長(zhǎng)期保持膜的運(yùn)行通量。
分離精度高。
運(yùn)行成本低。
4、經(jīng)濟(jì)效益
無(wú)需傳統(tǒng)廢水處理過(guò)程,可節(jié)省年廢水處理費(fèi)用80-100萬(wàn)元。
按照硫酸排放含量10%來(lái)計(jì)算,每噸價(jià)值約為100元以上,若每使用1000噸98%的硫酸,回收率以85%計(jì)算,則每年可節(jié)省成本90萬(wàn)元以上。效益合計(jì)為170-190萬(wàn)元/年。
本裝置運(yùn)行費(fèi)用約為50萬(wàn)元/年,可為公司創(chuàng)造效益120萬(wàn)元/年以上。并徹底解決了廢水污染問(wèn)題,實(shí)現(xiàn)了可持續(xù)發(fā)展。
5、膜分離法回收廢硫酸的特點(diǎn):
采用膜分離工藝回收硫酸中鐵離子濃度在0.8ppm以下,能滿足極板生產(chǎn)的質(zhì)量要求;
廢硫酸的一次回收率≥75%,總回收率≥85%;
內(nèi)化成廢硫酸回收前需稀釋,最佳的濃度應(yīng)為10%左右,稀釋用水應(yīng)使用無(wú)離子水或二級(jí)反滲透產(chǎn)水;
廢酸膜處理回收過(guò)程不需加入化學(xué)原料,無(wú)二次污染,大幅度降低了堿用量,節(jié)約處理成本。同時(shí)減輕了廢水處理負(fù)荷,減少了廢水中硫酸根離子,為實(shí)現(xiàn)廢水回用(零排放)提供了前提條件。
該技術(shù)工藝簡(jiǎn)單,運(yùn)行成本低,占地面積小,能實(shí)現(xiàn)連續(xù)運(yùn)行,便于操作和管理。因此該技術(shù)適用于鉛酸蓄電池極板生產(chǎn)廢硫酸處理回用。
該工藝按照資源化循環(huán)利用的原則,既實(shí)現(xiàn)了廢物回收利用,又可實(shí)現(xiàn)廢水零排放,徹底解決了鉛酸蓄電池極板生產(chǎn)廢水污染問(wèn)題,有著較好的經(jīng)濟(jì)效益和社會(huì)效益。
6、廢酸膜法處理回收工藝
目前主流的廢酸處置工藝主要分為四種:1.中和工藝、2.膜集成分離工藝、3.離子交換法、4.滲析法。
廢舊鉛蓄電池中硫酸重量約占蓄電池的15%,在使用、維護(hù)、回收、破碎過(guò)程中的不可預(yù)知的因素,其雜質(zhì)含量高,如Fe2+濃度約為1500mg/l,Cl-濃度約為20mg/l。目前常見(jiàn)的方法是采用石灰和液堿中和工藝。但作為廢電池回收和生產(chǎn)企業(yè),硫酸的使用量非常大,采用硫酸除雜回收工藝更為經(jīng)濟(jì)。
采用膜集成處理工藝,能有效去除硫酸中的Fe2+、Cu2+,Mn2+、等離子,經(jīng)過(guò)處理后可用于鉛蓄電池生產(chǎn)。
同時(shí),我們還可以根據(jù)客戶需求采用膜技術(shù)對(duì)酸進(jìn)行多級(jí)除雜,得到滿足客戶使用需求的高純度酸。
硫酸回收率≥85%,回收硫酸濃度12±2%(wt),F(xiàn)e2+濃度可≤1mg/l。
硫酸回收率高,實(shí)現(xiàn)了資源化再利用,大幅度減少了污染物排放量。與液堿中和工藝相比,運(yùn)行成本低,設(shè)備投資回收期短。
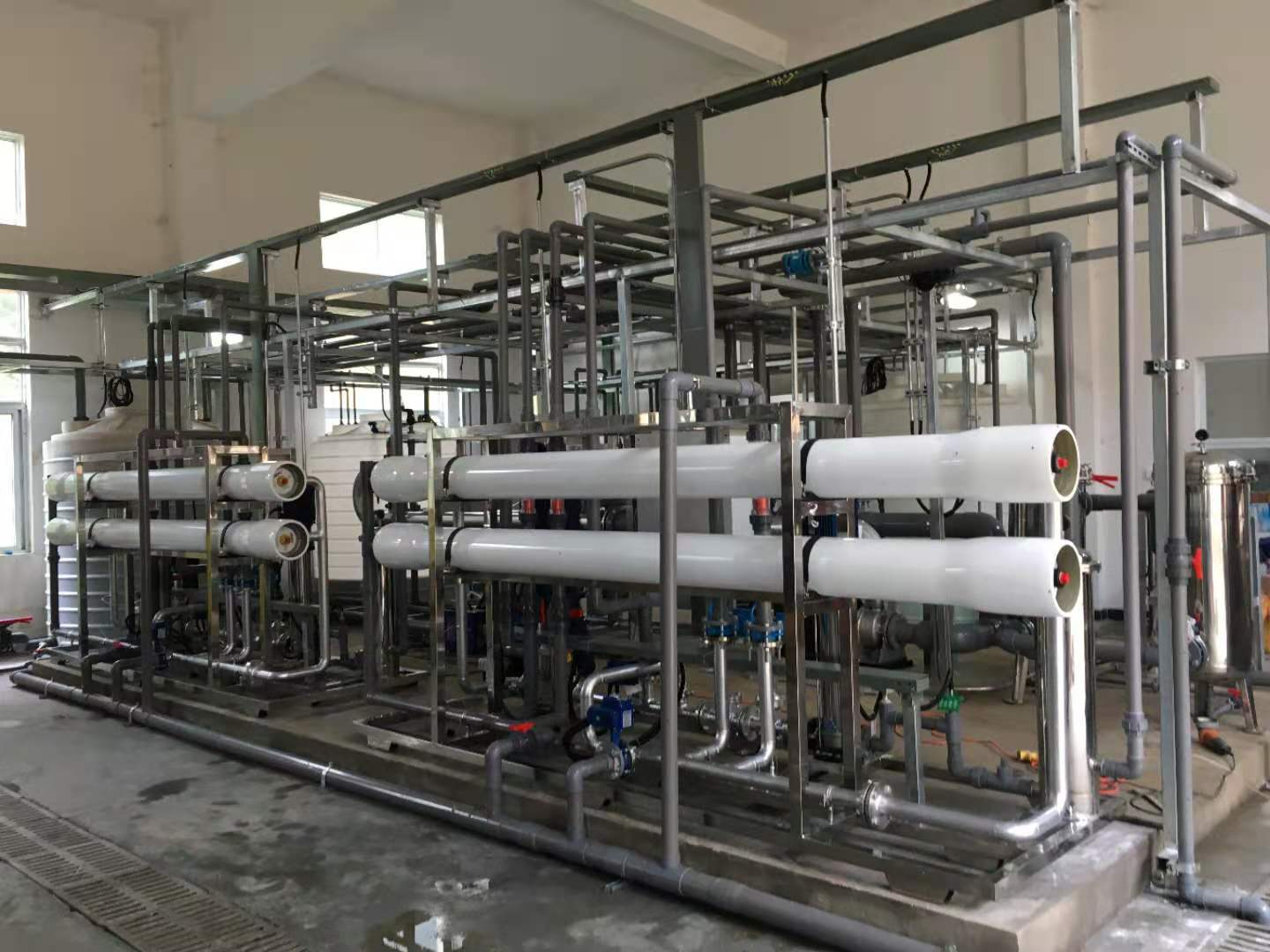
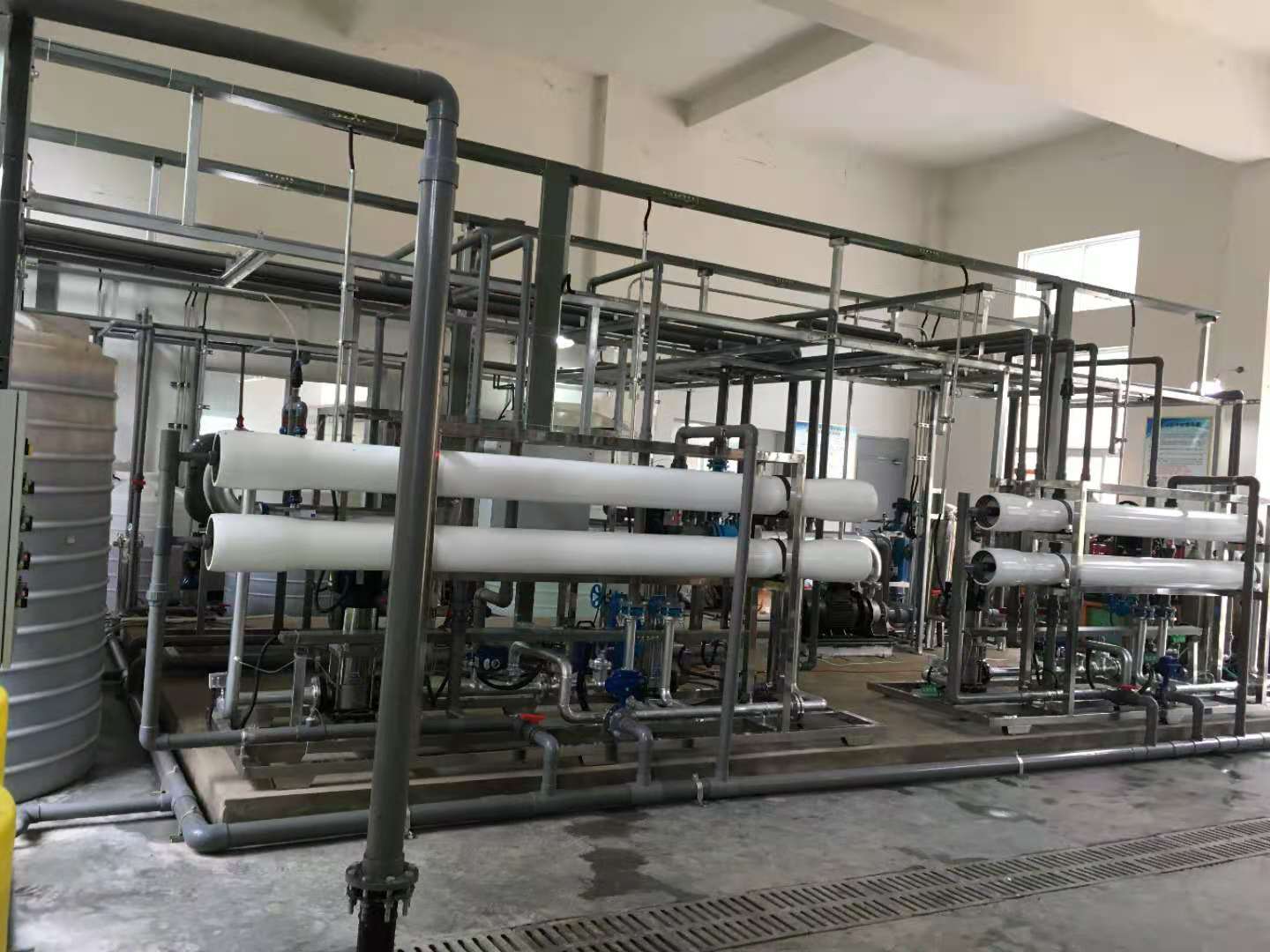
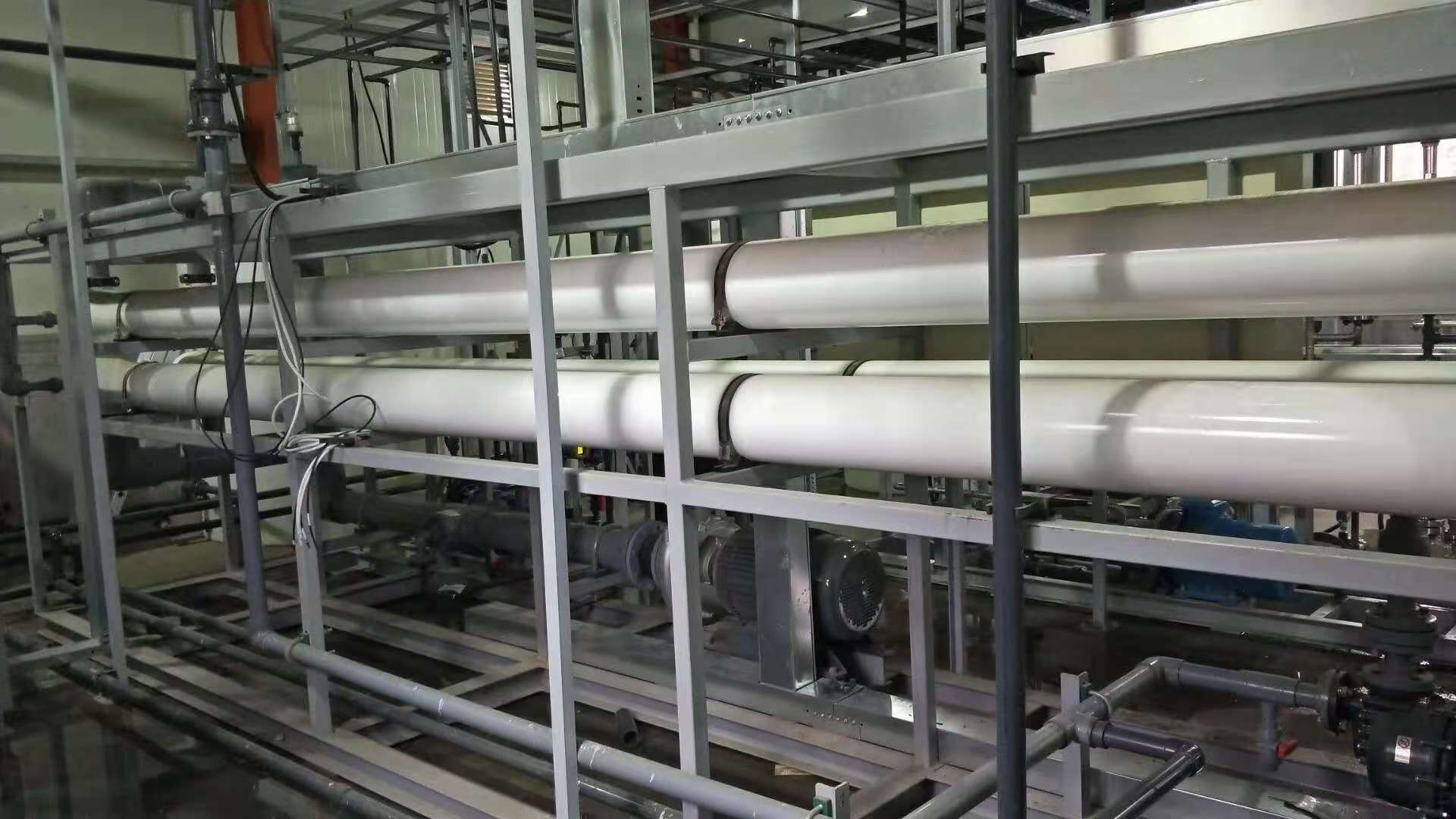